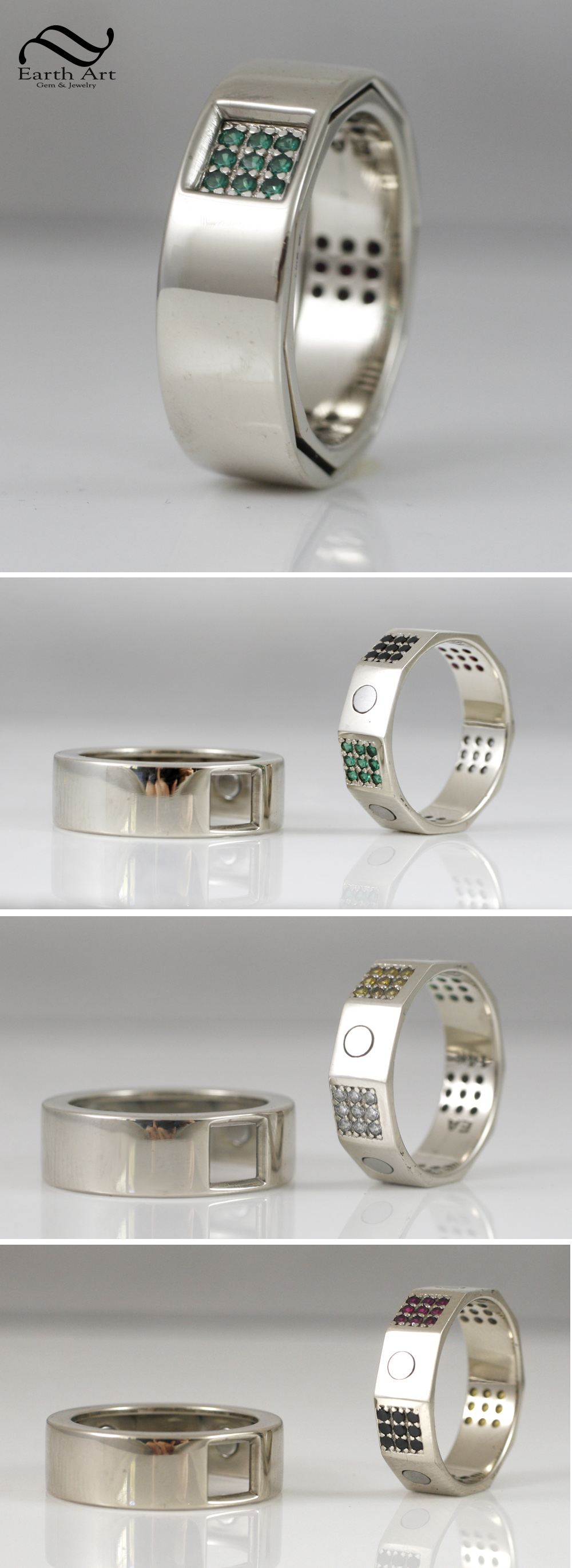
This was a really cool project. My client wanted a ring that could show a swatch of color, one color at a time, with 5 color options to choose from. We discussed multiple options, including plating, enamel and gemstones. I ultimately settled on gemstones as they were going to be the easiest to isolate and control and would mean the entire ring could be done in-house.
I used an array of 9 stones for each color. We opted for syntheyic gemstones rather than natural for this ring since they would have more color saturation in these smaller sizes than natural stones. In addition, getting 9 matched stones would be far easier. A larger gemstone would have provided more color surface area and less labor, but the stone would have been too deep.
The design I created was a 10 sided double ring. The inner ring held all 5 colors on alternating sides, and then rare earth magnets in the remaining sides. Everything was polished down flush. Even the gemstones! After setting them, I ground the surface of the stones and prongs down flush to create a totally flat plane that would allow the inner ring to slide into the outer ring without snagging. I used a series of diamond wheels and paste to then re-polish the stones surface, all the way to 50,000 grit!
The magnets were separated out into 5 pairs and the polarity was marked on each pair. Then I had to cross check each pair combination to make sure that the north and south poles on each magnet were all the same, so that as the inner ring was rotated around the outer ring, the magnets would all still pull as new pairs lined up.
The 10 sided design meant that in order to rotate the color, the inner ring had to slide out off the outer ring, rotated to the desired color, and then slid back in. One of the challenges was that the magnets were attracted to my regular tools such as my hammer, tweezers and bezel pusher. So I had to construct some rudimentary tools out of copper which is so weakly magnetic, that it did not attract the magnets. A dab of 2 part clear epoxy was added and each magnet was pushed into place. On the outer ring, I had to hold each magnet in place with tiny copper brackets that I created so that they would not slowly pull themselves out of their holes while waiting for the epoxy to set. (Each magnet wanted to pull out of its hole and across the ring to the other 4 magnets.) The inner ring was easier since each magnet also pulled inward but the ring was there, so they simply held themselves in place while the epoxy set up. Then I had to grind all of the magnets flush and polish the rings once again. With all the metalwork and polsihing complete, I gave the ring a thorogh cleaning and tested the fit and magnatism. Everything worked perfectly! This was one of my more challenging builds but very rewarding in the end. Getting a huge thumbs up from the client and his wife was the cherry on top!